Quality Assurance
- All parts ordered will be delivered on time, and beyond your expectations
- Compensation measures are available in case of any quality issues
- Support online remote check for acceptance Inspection
Table of Contents
Quality Standard
Tolerance Standard for CNC Machining
ISO 2768-1 defines general tolerances for linear dimensions as well as angular dimensions in CNC machining, such as external & internal size, step size, diameters, radii, distances, external radii and broken edge chamfers.
This standard covers 4 levels of tolerances.
If specific tolerances are not clearly indicated on the drawing, ISO 2768-mK standards will be followed by default.
- M – Medium tolerances
- F – Fine tolerances
- C – Coarse tolerances
- V – Very coarse tolerances
Permissible deviations for ranges in nominal dimensions (mm ) | Tolerance Class Designation (Description) | |||
---|---|---|---|---|
f (fine) | m (medium) | c (coarse) | v (very coarse) | |
0.5 up to 3 | ±0.05 | ±0.1 | ±0.2 | – |
over 3 up to 6 | ±0.05 | ±0.1 | ±0.3 | ±0.5 |
over 6 up to 30 | ±0.1 | ±0.2 | ±0.5 | ±1.0 |
over 30 up to 120 | ±0.15 | ±0.3 | ±0.8 | ±1.5 |
over 120 up to 400 | ±0.2 | ±0.5 | ±1.2 | ±2.5 |
over 400 up to 1000 | ±0.3 | ±0.8 | ±2.0 | ±4.0 |
over 1000 up to 2000 | ±0.5 | ±1.2 | ±3.0 | ±6.0 |
over 2000 up to 4000 | – | ±2.0 | ±4.0 | ±8.0 |
Permissible deviations for ranges in nominal dimensions (mm) | Tolerance Class Designation (Description) | |||
---|---|---|---|---|
f (fine) | m (medium) | c (coarse) | v (very coarse) | |
0.5 up to 3 | ±02 | ±0.2 | ±0.4 | ±0.4 |
over 3 up to 6 | ±0.5 | ±0.5 | ±1.0 | ±1.0 |
over 6 | ±1.0 | ±1.0 | ±2.0 | ±2.0 |
Permissible deviations for ranges in nominal dimensions (mm) | Tolerance Class Designation (Description) | |||
---|---|---|---|---|
f (fine) | m (medium) | c (coarse) | v (very coarse) | |
up to 10 | ±1º | ±1º | ±1º30′ | ±3º |
over 10 up to 50 | ±0º30′ | ±0º30′ | ±1º | ±2º |
over 50 up to 120 | ±0º20′ | ±0º20′ | ±0º30′ | ±1º |
over 120 up to 400 | ±0º10′ | ±0º10′ | ±0º15′ | ±0º30′ |
over 400 | ±0º5′ | ±0º5′ | ±0º10′ | ±0º20′ |
Tolerance Standard for Casting
The tolerances of die casting are determined by both the material and the manufacturing method.
The tolerances specification for metal alloy castings are indicated in ISO 8062.
General tolerance grades for castings are (CT) 7 to 12.
The tighter tolerances are available on case by case.
*Manual molding (CT9-CT12) | Semi-Automatic molding (CT9) | Horizontal molding machine (CT8) | Vertical molding machine (CT7) | Basic dimension (mm) |
1.5-4.2 | 1.5 | 1 | 0.7 | 1-10 |
1.6-4.4 | 1.6 | 1.1 | 0.78 | 10-16 |
1.7-4.6 | 1.7 | 1.2 | 0.82 | 16-25 |
1.8-5 | 1.8 | 1.3 | 0.9 | 25-40 |
2-5.6 | 2 | 1.4 | 1 | 40-63 |
2.2-6 | 2.2 | 1.6 | 1.1 | 63-100 |
2.5-7 | 2.5 | 1.8 | 1.2 | 100-160 |
2.8-8 | 2.8 | 2 | 1.4 | 160-250 |
3.2-9 | 3.2 | 2.2 | 1.6 | 250-400 |
3.6-10 | 3.6 | 2.6 | 1.8 | 400-630 |
4-11 | 4 | 2.8 | 630-1000 | |
4.6-13 | 4.6 | 3.2 | 1000-1600 | |
5.4-15 | 5.4 | 1600-2500 |
Tolerance Standard for Injection Molding
The deviation of injection molded parts from nominal dimensions usually depends on the manufacturing process used.
Therefore, the tolerance requirements need to be taken into account when selecting the process.
DIN ISO 16742 and DIN ISO 20457 will be applied to the tolerance standards for injection molding.
Rigorous Quality Control Process
Our commitment to high quality to our customers comes from the sum of our many years of production practice as well as responsibility to our customers.
Our quality management runs through every step of the process from raw material selection to final inspection.
When a purchase order is placed, we will select from a list of material suppliers and request material certifications, as well as issue incoming inspection reports.
If necessary, chemical tests or physical property tests of the materials are exerted.
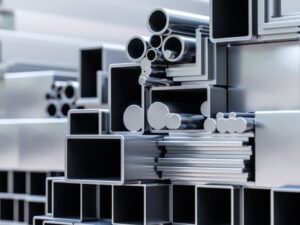
Our core technical staff has over 5 years of industry experience and they are skilled in manufacturing process optimization.
The accumulation of years of practical experience in production has led to their high productivity and low defect rate.

In addition to the optimization of manufacturing process , we upgrade our manufacturing facilities for specific parts with iterative batch production needs, such as customizing special machines, or equipping automated production lines to improve production efficiency.

From raw material procurement to production to shipment, each step is subject to multiple strict quality check.
And scientific quality control measures are used to achieve steady quality assurance, such as sampling inspection based on AQL and automated 100% full inspection.
Advanced quality control is a strong guarantee for batch production.

Quality Reports
To increase your confidence in our custom fabricated as well as prototype parts, we can provide appropriate test reports on request, showing that material quality and product performance meet expected requirements.
Certificates of Conformity
Final certificates by quality auditors that the parts made are in full compliance with the order specifications.
Material Test Reports
Tests exerted on purchased raw materials, such as chemical composition tests, physical property tests, etc.
Full Dimensional Reports
All dimensions of the parts made, especially critical dimensions, will be performed using micrometers, calipers or CMMs.
Material Certificates
Require material suppliers to issue material certificates for each batch, which can effectively trace the source of materials.
Inspection Reports
Through multiple strict quality inspection procedures, the defect rate is effectively avoided or minimized.
FAI Reports
First article inspection ensures quality consistancy in volume manufacturing by verifying specifications in advance.
Assurance Terms
We are committed to providing you with excellent service to boost your business.
To address your concerns and show our sincerity and ability, in case that the orders fail to cater to your expected requirements, we will process a rework or refund without hesitation.
The wishes of our clients will be put first.
Terms for Reprocess
- Unacceptable surface defects
- Fail to cater to specified tolerance criteria
- Unqualified materials
Terms for Refund
- The part can not be reprocessed
- Rework can not be accepted
- Other reasons