Die Casting Manufacturer
in China
- Tolerance down to ± 0.1 mm (0.004”)
- Rapid tooling, with multi-cavity mold available
- Low MOQ, and 100% guaranteed quality

Die Casting Service

If you have design requirements for complex parts, we can help you bring it to life.
From tooling design to finishing, we promise that every order will be delivered on time with high quality.
We serve a wide range of industries including automotive, mechanical, medical, electrical, energy, aerospace, communications and more.
Our expertise and experience enable us to offer you die castings with tight tolerances, minimum draft angles, excellent finishes or minimal wall thickness at a lower cost.
Parts Show
Gallery of Die Casting Parts
As a precision die cast manufacturer, we are able to supply various die casting parts of superior quality.
In order to achieve a better aesthetic requirements, post-processing and finishing is the most vital step in precision die casting.
Among them, machining will be used to achieve precision requirements for the cast blanks, and finishing primarily be applied to remove surface defects from the die casting parts, and improve visual appearance.
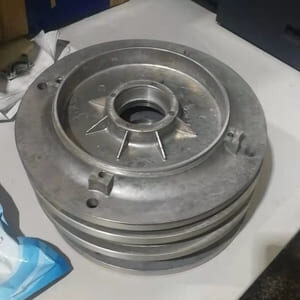
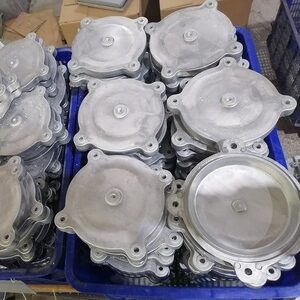
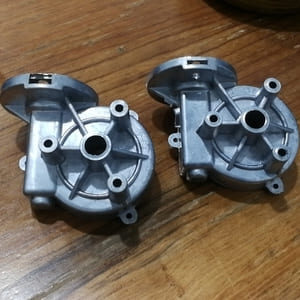
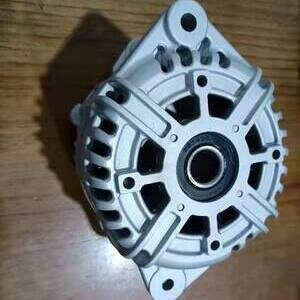

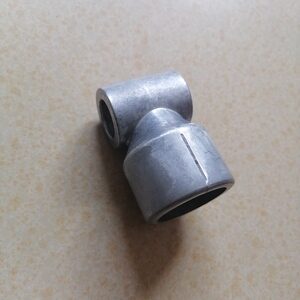

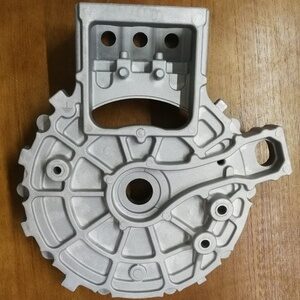
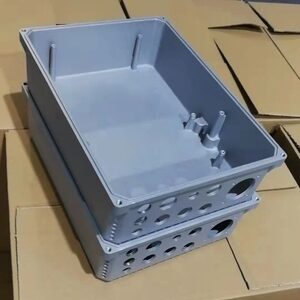
Post Processing Options
- Heat treatment, vaccum impregnation
- Machining and polishing process
- Part marking on request
- Cleaning, deburring, trimming
- Other finishing
Casting Capabilities
- Part weight: >=0.02 kg, <=12 kg
- Minimum part size: 17 × 4 mm
- Maximum part size: 300 × 650 mm
- Wall thickness: >=0.8 mm, <=12.7 mm
- Mold life: replacement free of charge
Material Selection
Materials for Die Casting Parts
As a common custom cast process, die casting is particularly suitable for parts with complex structures.
Generally, Non-ferrous metals with low melting temperatures are used to make die-cast parts, such as zinc, copper, aluminum, magnesium, and lead.
The following will explain the materials used in most die casting processes.
Aluminum die casting alloys exhibit high thermal conductivity, electrical conductivity, and cutting performance.
In addition, due to the low density and high strength of aluminum alloys, they can maintain good mechanical properties at high or low temperatures.
Commonly used aluminum alloys: A360, A380, 383, B390, A413, and CC401.
Zinc alloys are more cost effective and stronger than other similar alloys.
It also has better fluidity and corrosion resistance, so they are used primarily in die-cast instruments, auto parts housings and other complex metal parts.
Commonly used zinc alloys: Zamak-2, Zamak-3, Zamak-5, Zamak-7, ZA-8, ZA-12, ZA-27
Magnesium die casting alloy has the advantages of high strength, low viscosity, good fluidity, corrosion resistance, easy to fill complex cavities, often used for die casting of molds and thin-walled parts without thermal cracks.
Commonly used magnesium alloys: AZ91D, AM60B, AS41B
Copper has the ability to resist wear and tear.
It is also widely used in die casting. The advantages of copper are many, mainly as follows:
- Excellent electrical conductivity
- Dimensional steadiness
- High strength
DFM Advice for Die Casting
Weight Reduction
Aim to reduce the weight of the material to save costs of die cast.
Ribs
Make sure that ribs must be added to the thin walls during design.
Shrinkage
Apply draft angle into die casting parts so as to reduce shrinkage.
Surface Finish
Well polished tooling will help in die castings with good surface.
Draft Angle
The draft angle is a small taper on the side of the die cavity helps in the ejection of casts.
Cross Sections
Uniform cross-section helps to speed up the metal flow through the die cast mold.
Radii and Fillets
The outer corners should be designed as radius as possible, the inner corners with fillet.
Wall Thicknesses
The uniform walls allows for smooth metal flow during filling and reduces distortion.
Parting Line
Careful consideration should be give to parting lines so as to keep it straight or flat if possible.
Ejector Pins
Reasonable placement of the ejector pin so that the castings will be ejected cleanly without damage.
Multi-cavity die
A multi-cavity die cast tooling can save cost, since one production cycle can make multiple parts.
Gas Porosity & Blister
Can be avoided by changing the runner and gate, improving the venting and adding vacuum to the die.
Why Choose Us For Die Cast Parts
DFM Advice
Die casting defects are unacceptable, and it becomes important to optimize its design before the die casts are manufactured.
Our experienced team will apply DFM best practices to develop optimal die casting solutions, along with sound technical advice and cost-saving methods.
quick quote
We have the ability to quote quickly, and submit it within 12-24 hours. Shipping costs and lead time will also be estimated in real time on request for your reference.
scalability
We have the flexibility to support you from tooling design & fabrication, rapid prototyping to volume manufacturing, and support multi-cavity mold according to the actual requirement.
competitiveness
Every stage, from raw material sourcing to production and quality control, is optimized to achieve the best cost control in the die casting industry, while we maintain only a lower reasonable profit to sustain company operations.

Versatility
With a full range of technology, we can offer you one-stop customized die casting services with diverse surface finishes to meet your various cosmetic appearance needs.
responsibility
Each order is subject to at least three quality checks to ensure high-quality, and every work given by the customer is completed carefully and the work progress is kept informed in anytime.
Surface Finishing
For die casting parts with cosmetic requirements, we also support a variety of surface finishes including powder coating, anodizing, bead blasting, electroplating, brushing and part marking.
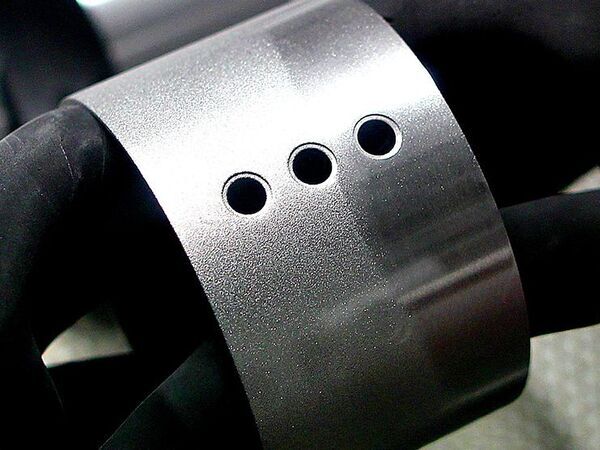
Bead Blasting
If aesthetic is essential, bead blasting is the finish we prioritize. Parts can be bead blasted from #60 grit to #200 grit.
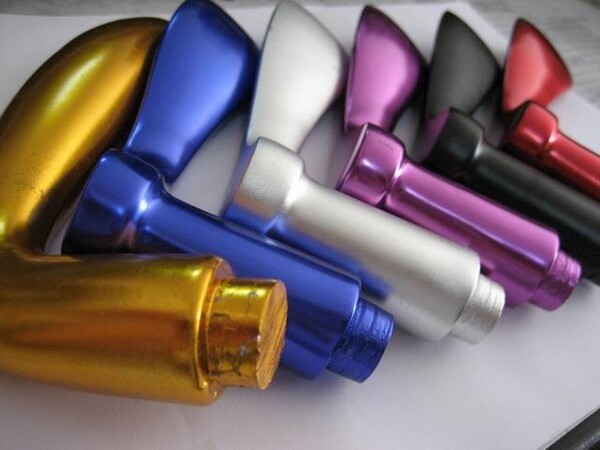
Anodizing
Resistant to corrosion and oxidation, has a great color and a uniform, clean, matte or glossy appearance.

Electroplating
With great looking and corrosion resistance, such as silver, gold, nickel, zinc or chrome plating, etc.
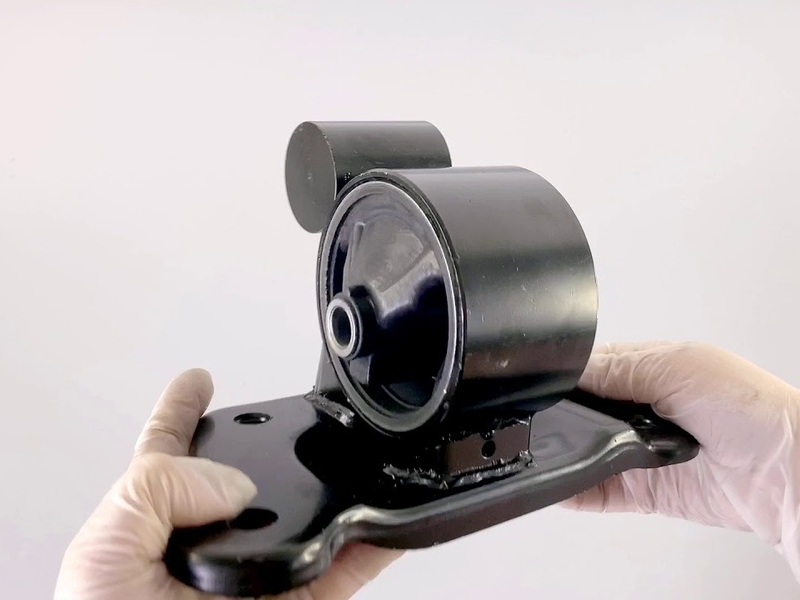
Electrophoresis
Electrophoresis is applied to a metallic luster and an unlimited range of colors. It improves the surface properties and corrosion resistance of metal alloy parts.

Brushing
Brushing is a surface finishes process in which abrasive belts are used to draw traces on the surface of a material, usually for cosmetic appearance.
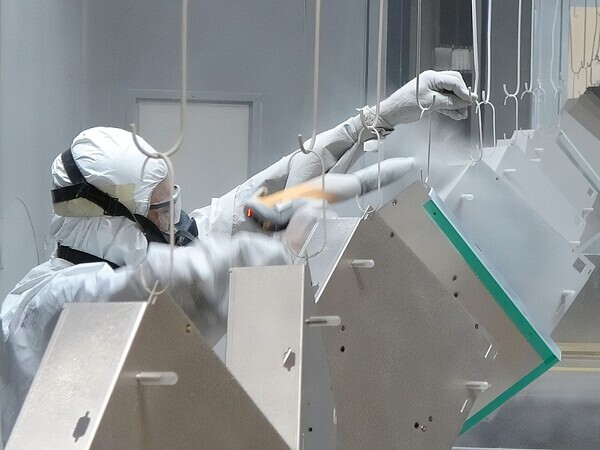
Powder Coating
Powder coating can be used to spray a free-flowing and dry powder to parts, and allows for a very uniform look with great corrosion & wear resistance.
Defects in Die Castings

We summarize the common defects in the die casting process (mainly occurring when the molten material is filled and cooled) and aim to eliminate or minimize them in castings by studying their causes and remedies.
These defects are divided into two categories according to the location where they occur, namely internal defects and surface defects.
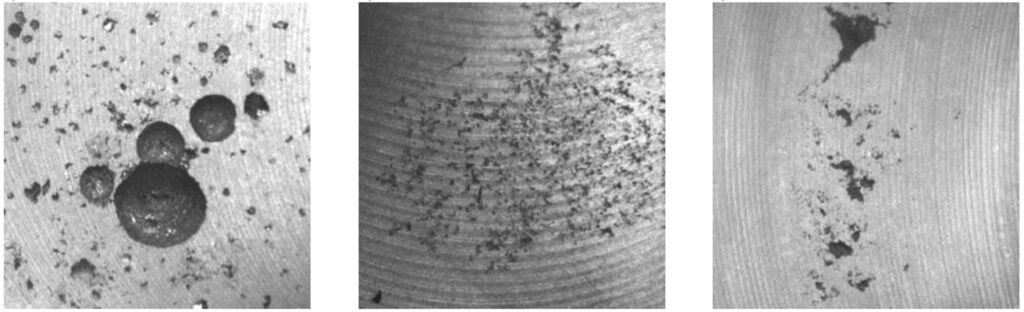
Internal defects in die castings
These types of defects are not easily detected, due to occurring inside the castings.
They affect the internal structural stresses of the castings and reduce their physical properties.
- Gas porosity
- Inclusions
- Shrinkage porosity
Superficial defects in die castings
These types of casting defects usually occur on the surface of the castings and, therefore, they are visible.
However, they damage the surface of the castings and interfere with their visual appearance.
- Cold laps
- Flashes
- Flow marks
- Drags
- Blister
- Lamination
- Lakes
- Cracks
Industrial Applications for Die Casting
Automotive Parts
There are numerous applications, including motor brackets, engine parts, stator, electronic covers, heat sink, chassis parts, cylinder heads, etc.
Telecom components
Common applications in the communications industry include from 5G base-station housings to enclosures for various telecom products.
consumer electronics
Die cast is commonly used in components for all these products in the electronics industry from 5G base station housings, drones, smart phones to appliances.
Health Care Industry
Die casting process is also applied to medical devices like ultrasound equipment, dialysis equipment, gearboxes for hospital beds and pacemakers.