If you’re like most people, you probably think of CNC turning as something that only happens in factories. You may be surprised to learn that CNC turning is now becoming popular among wood and metalworkers.
With the help of CNC lathes or CNC turning centers, you can turn almost any material into beautiful works of art. In this comprehensive guide, we will teach you everything you need to know about Computer numerical control (CNC) turning, from choosing the suitable machine to mastering the basics of the craft. Read on!
What Is CNC Turning?
Unlike rotary cutting tools, a non-rotary one is used in the CNC turning process to create a helix path. “CNC” is “computer numerical controlled”, meaning that a computer program controls the turning process. Some examples of products that can be made using CNC turning machines are shafts, rollers, and tubes. You can use these machines not only to cut workpieces but also to trim them or drill holes into them. You can also cut threads on screws or bolts.
CNC turning creates parts with multiple dimensions by using a computer to control the movement of tools. It is often used in conjunction with other machining processes such as CNC milling and CNC drilling to create complex products. Materials that can be CNC-turned include plastics, metals, and composites. The type of material used for CNC machining turning depends on the application and desired properties of the end part.
Common Types of CNC Turning Operations
There are different types of turning operations, each designed to perform a different task. They include:
1–Turning
To turn the workpiece, lathes or CNC turning centers are used. The machine holds and rotates the workpiece during cutting. These CNC lathes use computer-aided design to create a variety of shapes.
As the most common machining and manufacturing process, turning and milling are completely different. In contrast to any other manufacturing process, turning is the removal of a rotating workpiece with a cutting tool that remains stationary.
Turning is typically used to create cylindrical parts with circular cross-sections, but it can also produce parts with non-circular cross-sections. Having the cutting tools remove material from the workpiece’s circumference all at once, makes it more efficient.
Here below are four main types of turning operations:
Step turning
It is the operation in which a component will be cut into various diameter steps over a given length, using a single-point cutting tool, known as step-turning.
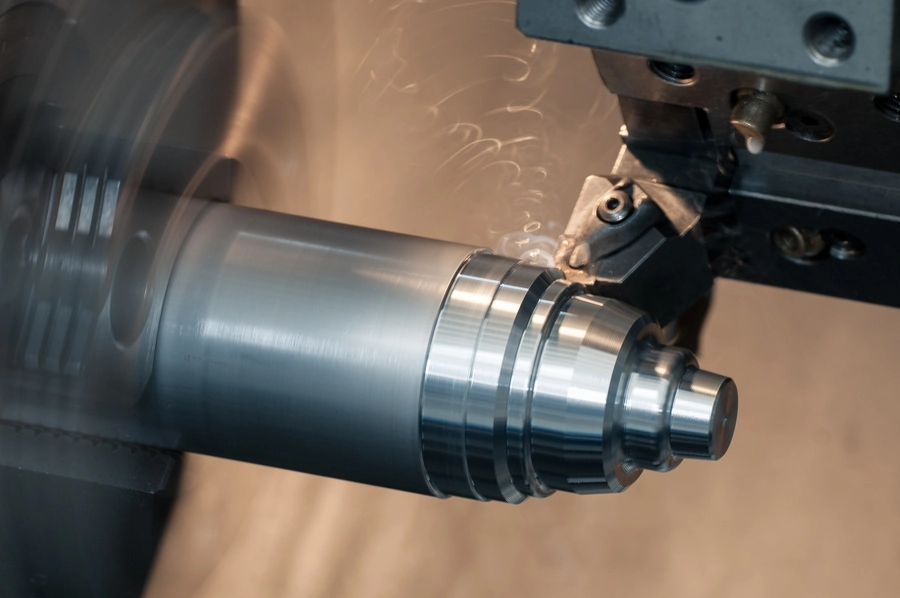
In step turning, since different diameters are to be machined at different positions on the workpiece, in order to increase efficiency and ensure accuracy, roughing should be first used to remove the largest amount of material, and then finish machining for the remaining machining allowance.
Tapered turning
The technique of tapered turning consists of shaving down the diameter of a cylindrical workpiece so that it’s smaller at one end than the other. This can be done either externally or internally, depending on the desired final shape. External tapers are typically used for decorative purposes, such as tapering the end of a Dowel pin.

Internal tapers are used when it is necessary to create a seal, such as in hydraulic cylinders. When creating an internal taper, it is essential to ensure that the smaller end’s ID is large enough to allow for smooth movement. If the ID is too small, the parts will have excessive friction and wear.
It is also essential to consider any length reduction when designing an internal taper, as this will affect the overall dimensions of the final product.
Spherical turning
This is also referred to as the “ball turning process” and is used to create parts with a curved surface. The workpiece is mounted in a three-jaw chuck to perform this operation and moves continuously while the cutting tool is stationary.
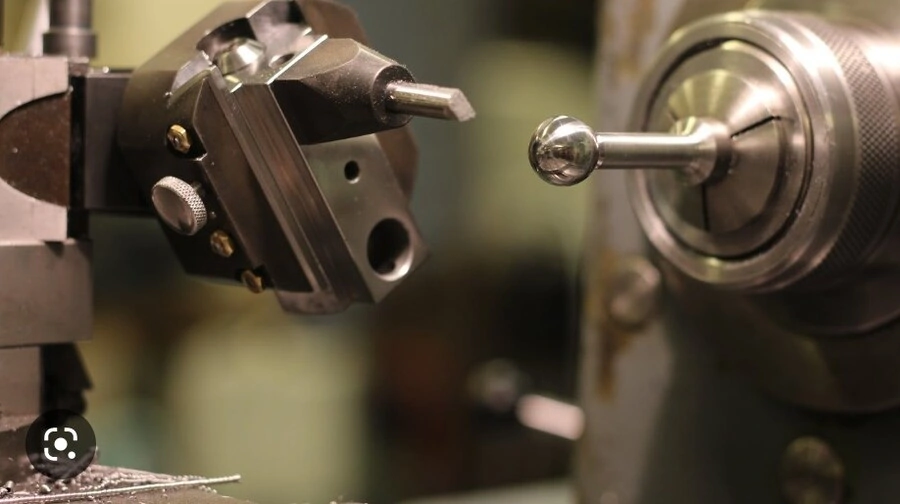
The cutting tool follows a pre-defined path to create the desired curvature.
This process can create spherical parts, such as spheres or cones, and curved surfaces on flat pieces.
Hard turning
This process is for finishing cylindrical parts with high hardness values. The method uses single-point turning tools with hardness values above 45 HRc. They are most commonly used on 58-68 HRc materials.
The cutting tools used in hard turning are more complex and wear-resistant materials than those used in conventional turning.
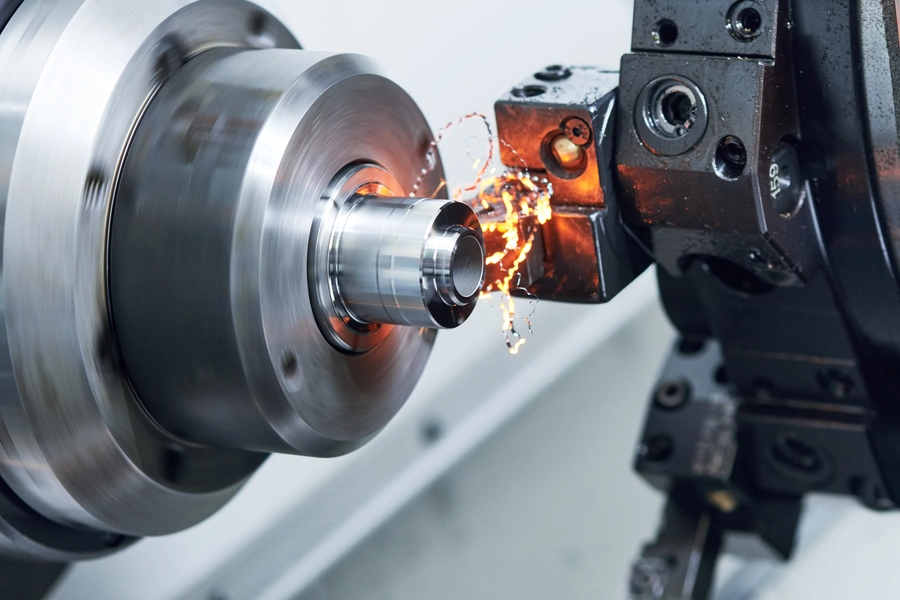
The cutting speed, feed rate, and depth of cut are also lower than in conventional turning. This machining process can be completed on CNC lathes or CNC turning centers.
It is an alternative to grinding for finishing parts with high hardness values. Hard-turned surfaces have good dimensional accuracy and surface finish.
2–Threading
Threading uses a single-point tool to create a threaded surface on a cylinder or cone. The device moves straight, while the workpiece’s rotation regulates how much thread is produced.
This process is usually used to create threads on the outside surface of a cylindrical workpiece.
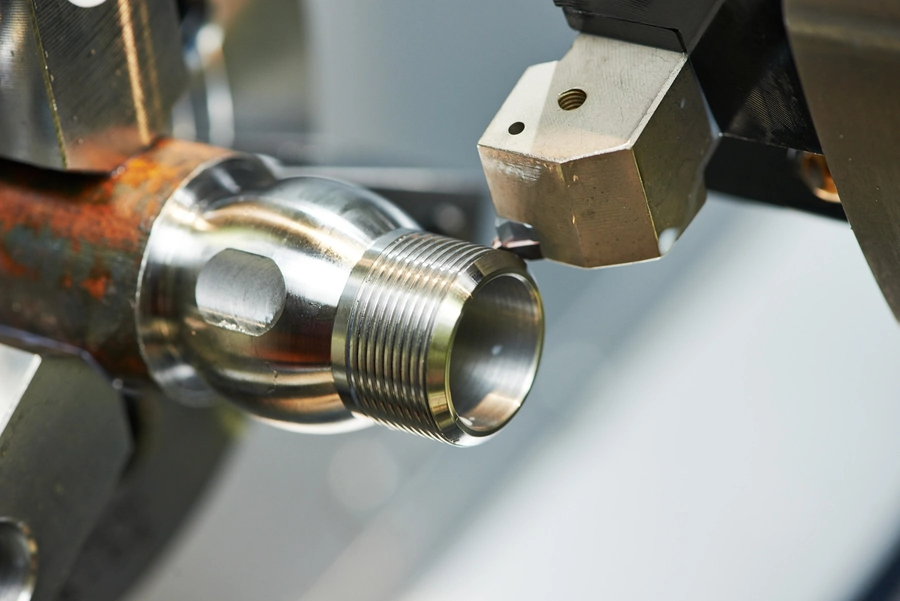
In addition to external threads, it can also be used to create internal threading on the interior surface of a workpiece. In addition, threading can produce taper threads, which get progressively smaller in diameter towards one end.
To perform this type of threading, the tool must be moved diagonally along the axis of the workpiece while it is being rotated.
3-Boring
In this process, the cutting tool moves along the surface of the workpiece, enlarging or finishing the internal diameter of a cylindrical hole.
The operation can be performed on external and internal surfaces, although it is more common to bore holes to enlarge an existing opening.
Boring is usually performed using a rotating cutting tool, such as a drill bit or end mill, although it can also be done with a non-rotating tool.
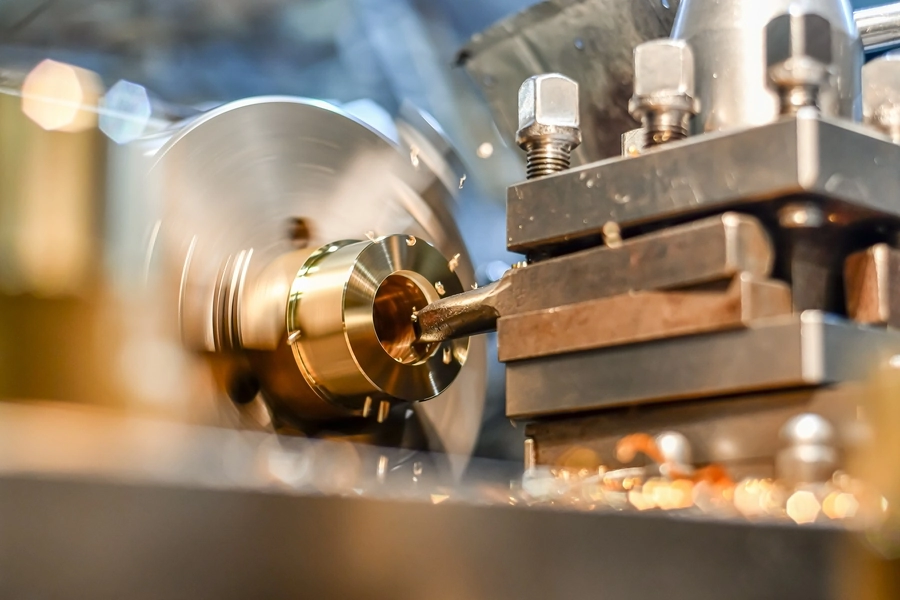
The cutting tool is attached to a spindle that’s run by a motor, and the object being cut is placed on a table that can move along the axis of where it’s being cut.
The cutting tool’s speed and feed rate are carefully controlled to avoid damaging the workpiece or breaking the device. Boring is often used to prepare holes for other machining operations, such as tapping or reaming.
4–Tapping
Tapping is cutting internal threads into a hole using a tap. The tap has several flutes that cut the threads as the tool is rotated in the workpiece.
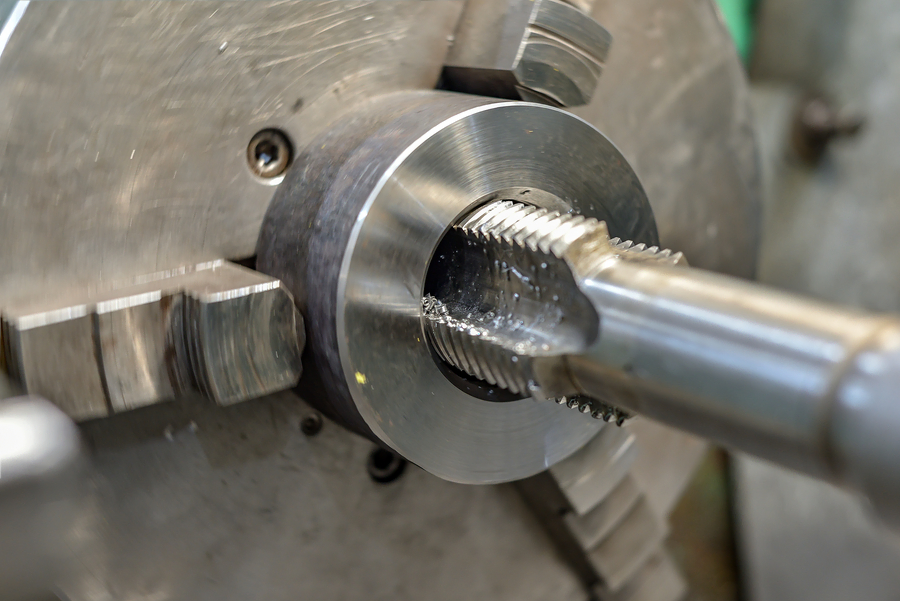
The tap must be of the correct size and type for the thread being created, as well as the material of the workpiece.
Tapping can be done manually or with a tapping machine, depending on the complexity of the operation. Special coolant is often used to reduce the cutting force and heat generated.
5–Drilling
The drill bit is mounted on a drill press, and the workpiece is mounted on a table that can move along the hole axis.
The drill bit rotates at high speeds and is advanced into the workpiece at a controlled rate.
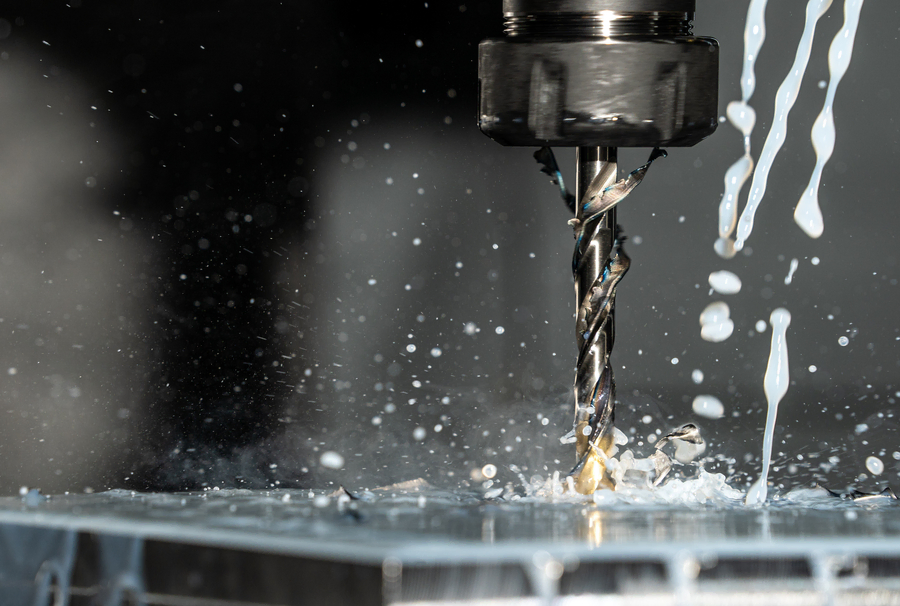
Drilling can create holes of various sizes and shapes, including round, square, and rectangular. It is also used to develop counter-sunk spots, tapered holes, and blind or through holes.
6–Reaming
Reaming is a finishing process that uses a reamer to create an exact-sized hole. The reamer’s cutting edges are finely honed and will not cause further hole enlargement. It improves the surface finish, roundness, and straightness of a pre-drilled hole.
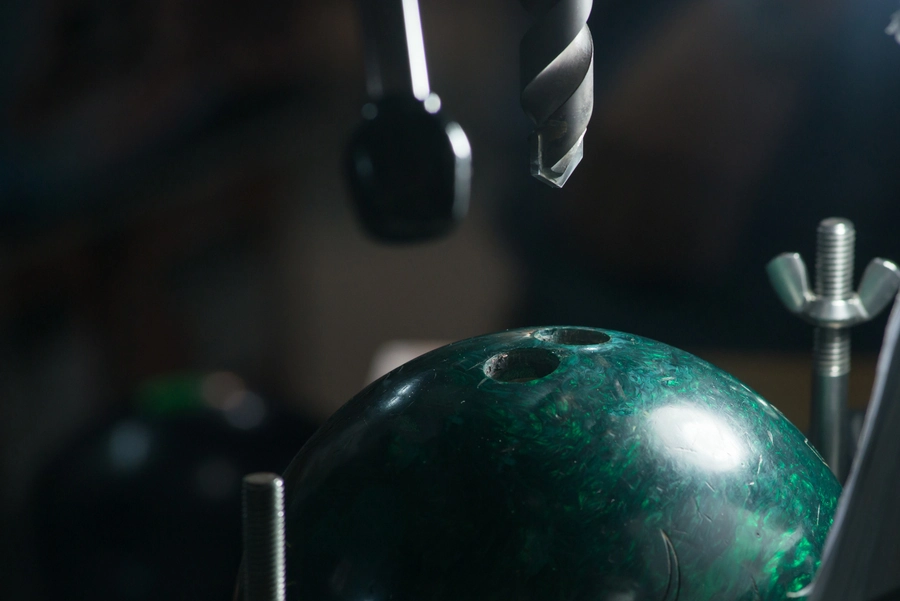
Reamers are available in various shapes, sizes, and materials to suit different applications.
7–Parting
When using lathe parting, the cutting tool should be mounted on the tool post and adjusted for height. The cutting depth must also be set before beginning a cut. It should be oriented perpendicular to the workpiece.
Then the cutting tool moves along the longitudinal axis of the workpiece and cuts a groove in the material. It should follow the same path on all passes, gradually deepening the groove until it reaches the desired depth.
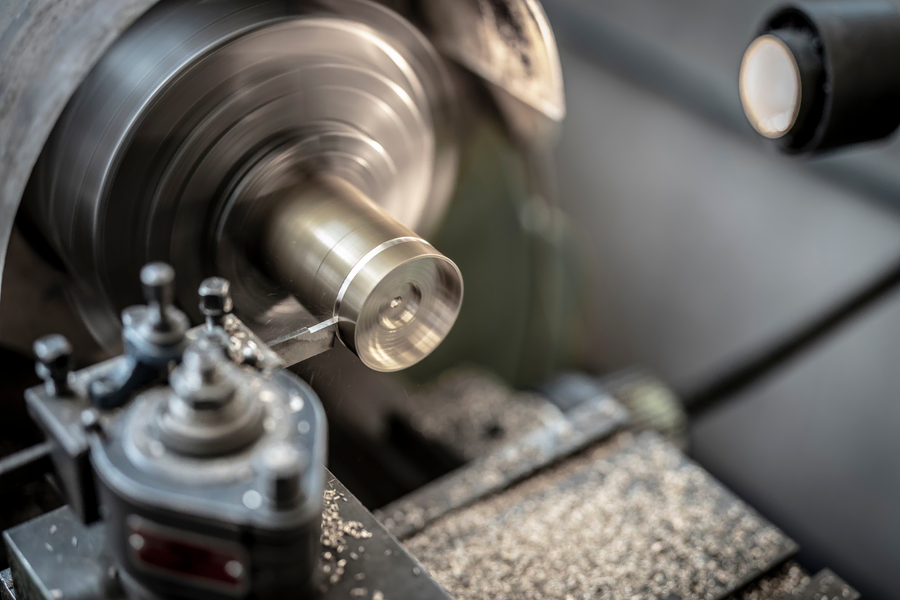
Parting can also be used to remove material from a workpiece’s outside diameter or create an internal shoulder. Parting tools are generally made from high-speed steel or cemented carbide and have a positive rake angle and round nose geometry.
When selecting a parting tool, it is essential to consider the depth of cut, feed rate, and speed. Parting is typically performed at slow speeds with light cuts to avoid chatter and heat build-up.
8–Facing
Facing is another machining operation that can be used to shape a workpiece. In this process, the cutting tool is fed in a radial direction across the face of the workpiece. Depending on the desired end shape, the tool can be fed in either a clockwise or counterclockwise direction.
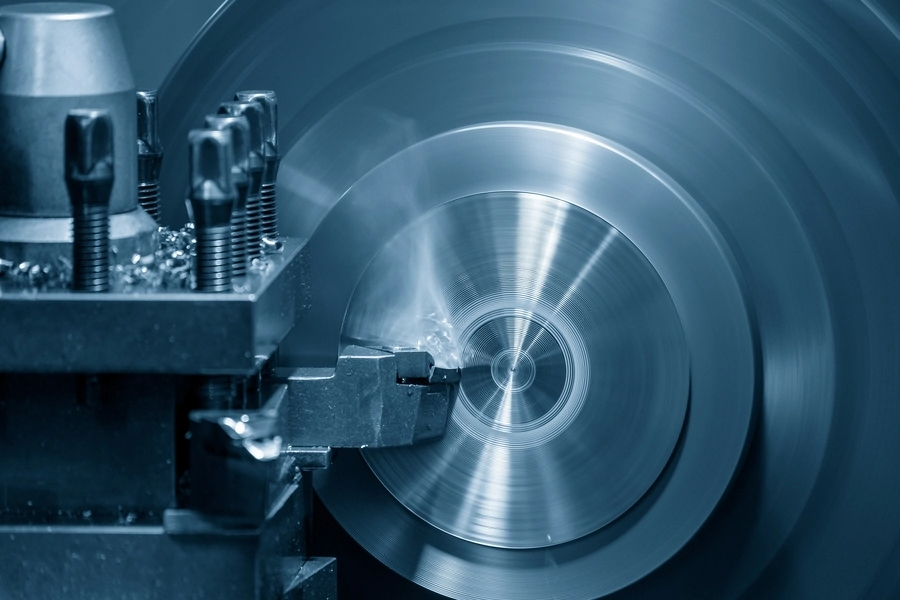
The cutting tool should be fed at a slow and steady rate to avoid chatter, which can cause an uneven surface finish. The feeding speed should also be adjusted to maintain the desired shape.
Once the facing operation is complete, any burrs should be removed with an appropriate deburring tool.
9–Grooving
This process can be performed with various tools, such as an end mill, parting tool, or forming tool to create a narrow cut.
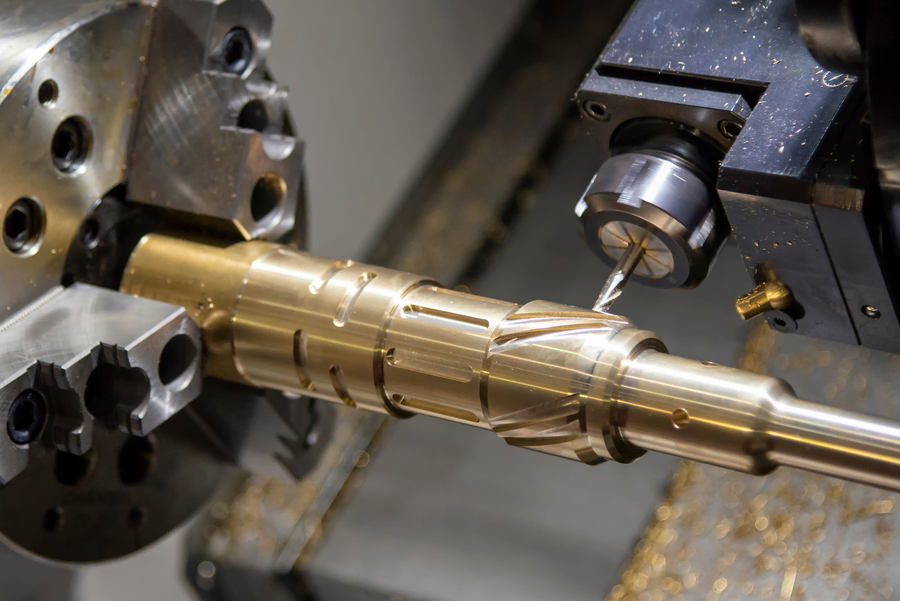
The cutting tool is advanced along the axis of the groove and cuts a channel or slot in the workpiece.
Grooving can be used to create a variety of shapes and can also be used to form internal or external threads.
The speed, feed rate, and depth of cut must be carefully controlled to achieve the desired finish.
10–Knurling
A knurling tool has two cutting wheels, which are pressed into the workpiece and rolled along its surface. It creates different patterns and shapes.
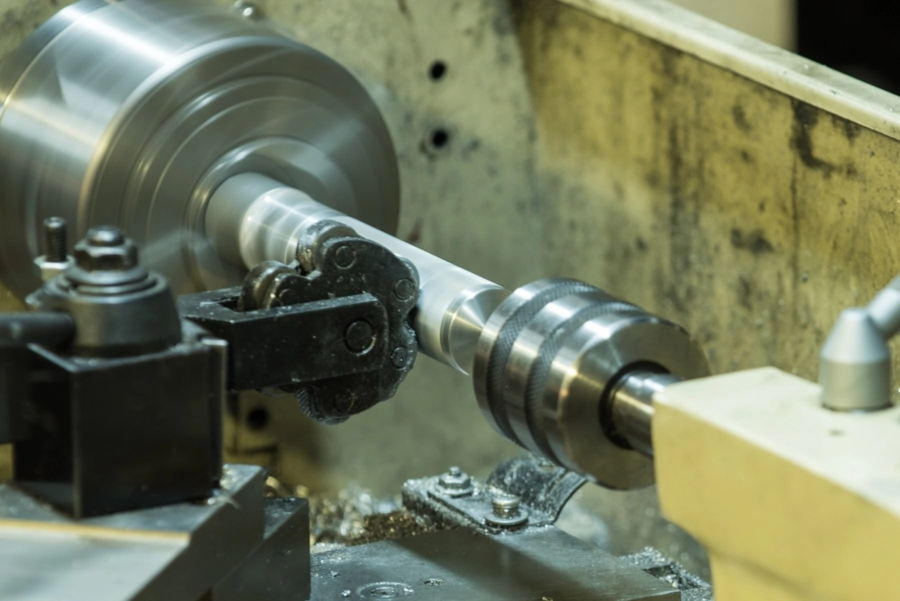
This process creates raised ridges or patterns on the surface of the workpiece without affecting the overall diameter or shape. It is most commonly used to provide a better grip for a handle or knob but can also be used to create decorative patterns.
Pros & Cons of the CNC Turning Process
Pros
- CNC turning is a precise process that can produce high-quality results.
- The process can be repeated repeatedly to produce identical parts.
- The adaptability of CNC turning allows manufacturers to produce an array of items.
- The process is fast and efficient, resulting in less waste material.
- CNC turning is a relatively straightforward process to learn and operate.
Cons
- Unlike CNC milling, it is only suitable for machining workpieces with symmetrical structures and can be rotated, so it is not used for workpieces with more complicated geometry.
- The process can be expensive, as it requires specialized machinery and tools.
- The results can be inconsistent if the operator is not skilled or experienced.
Key Considerations to Make CNC-Turned Parts?
To make quality CNC-turned parts, the following key considerations should be taken into account:
Threading & grooving
When creating threads and grooves, make sure that the tool is correctly positioned. Also, ensure that the cutting depth is correctly set to achieve a clean and accurate finish.
Cavities & Holes
Cavities and holes should be accurately drilled and reamed to avoid any misalignment. If a workpiece is too large for the CNC milling or CNC turning machine, a rotating tool, such as a lathe, can be used to complete the job.
When creating holes, the cutting speed and feed rate should be adjusted to achieve a smooth finish.
Tight tolerances
Tight tolerances require precise measurements and a skilled operator. After machining, measuring internal and external diameters is essential to ensure they match the desired specifications.
Thin Walls
Thin walls and sharp edges can be difficult to achieve with CNC-turning. Specialized tools, such as ball-end mills, must be used to achieve the desired result. To avoid heat build-up, use slower speeds and lighter cuts.
Length-to-diameter ratio
This is the most important consideration when machining a workpiece. If the ratio is too high, the material may be too weak and easily break during operation. A good rule of thumb is to keep the length-to-diameter ratio as low as possible.
Corner radii
When you create corners and internal radii, please use a tool with the correct radius. A large radius will reduce stress on the material and allow for smoother bends. If a smaller radius is required, it may be possible to use a unique tool or re-grind the cutting edge.
When Should You Use CNC Turning?
When the design of the workpiece can be achieved using both CNC turning and CNC milling, priority should be given to CNC turning because it has more advantages in terms of cost and accuracy generally.
There are three main periods or durations when CNC turning is the best option:
- When speed is the priority, and there is a need to complete the project in the shortest time possible.
- When accuracy is paramount, any mistakes could be costly.
- When there is a large production run, manual labor would be too slow or error-prone.
Industrial Applications of CNC Turning
Automotive
CNC turning has helped to revolutionize the automotive industry, as it allows for rapid prototyping of new parts and components. CNC turning is perfect for creating prototypes because it can produce complex geometries quickly and with great accuracy, thereby saving time and money in the long run.
CNC turning also allows for the mass production of automotive parts with reduced lead times and improved cost efficiency. This method of machining is used across the automotive industry to create a variety of parts, from engine components to body panels.
CNC turning machines can also be programmed with specific parameters for a particular part or component, ensuring consistency during production.
Medical
In the medical industry, CNC turning is used to create implants and prosthetics, as well as instruments and equipment.
The precision of CNC turning allows for the creation of tight tolerances and detailed features that are essential in medical applications.
In addition, the repeatability of CNC turning ensures that each part is identical to the next, which is critical when mass-producing medical devices.
Electronics
In Electronics, there are many components that need to be machined with precision, such as connectors, terminals, and pins.
With the use of CNC turning, these components can be created with intricate details and tight tolerances. This makes them ideal for a variety of electronic applications, from cell phones to advanced engineering projects.
Consumer Goods
CNC turning is also used to create consumer goods such as toys, sporting equipment, and jewelry. The finely-detailed workmanship of these parts necessitates accurate machining, a service that CNC turning can provide.
In addition, the repeatable accuracy of this machining process ensures that each part is identical to the next. This makes CNC an excellent option for a manufacturing process or creating consumer goods requiring high levels of detail and accuracy.
Machinery & Equipment
Large equipment and machines require components that are precise and accurate.
CNC turning is ideal for creating these parts, as it can produce complex geometries with tight tolerances. This makes it ideal for creating components for a wide range of machines and types of equipment, from construction machinery to military vehicles.