What Is CNC Milling?
CNC milling is a popular CNC machining process involving removing the material from a stationary workpiece through a rotary cutting tool. The process is carried out under computer control using CAD and CAM software.
Therefore, it ensures high accuracy and precision of complex parts. The rotating cutting tool exhibits a cylindrical shape and shows movement along different axes for the material cutting. The following three steps are involved in the CNC milling process.
Step 1: Generation of CAD model
Initially, the corresponding 2D or 3D CAD models are designed for the end product.
The resulting 2D and 3D models possess the following features.
- Constructions lines
- Threads indications
- Tolerances
- Dimensions of components
Step 2: Exporting CAD model to a CNC-Compatible File
In this step, the 2D or 3D design is exported to the CNC-Compatible file format.
It is a mandatory step because the CNC milling machines cannot properly understand the design until it is in the form of a CNC-compatible file format. For this purpose, you can use CAD software.
Step 3: Setting up and execution of CNC milling machines
This step includes attaching the cutting tool to a rotating spindle by the operator, and the workpiece is positioned on the table. After the setups, the milling operation begins.
The material is removed from a workpiece to create the desired end product, such as grooves, slots, and flat surfaces.
Types of CNC Milling Operations
Turn Milling
Turning and milling is a compound cutting operation done simultaneously in one machine. The tool is designed in such a way that milling and turning are combined.
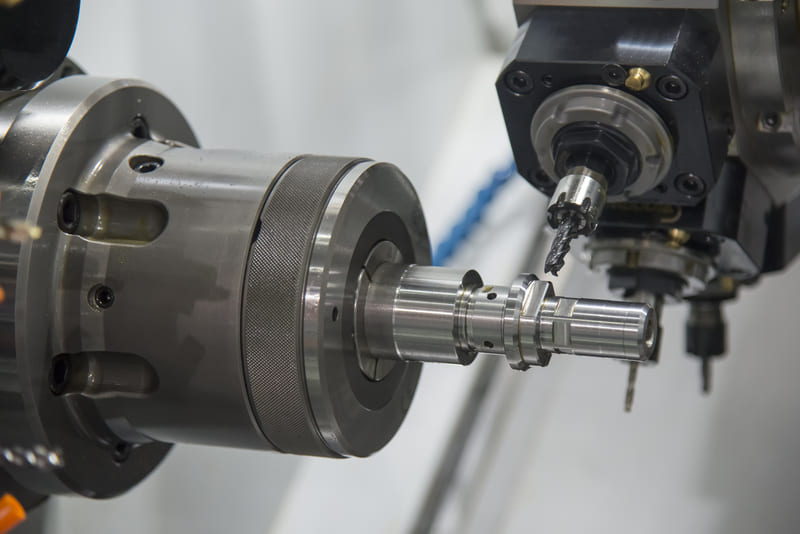
It offers the following advantages:
- It enhances overall productivity.
- The tool provides an excellent surface finish.
- It lessens the chances of wear of cutting tools.
- It helps in saving processing costs.
- This process aids in reducing clamping times.
Chamfer Milling
Chamfer milling also called chamfering, is a machining process in which a tiny section of the material is cut down from the machined part.
The material cutting is done at a particular angle. As a result, the produced surface is called chamfer. Its main purpose is to prepare workpiece edges for brazing or welding.
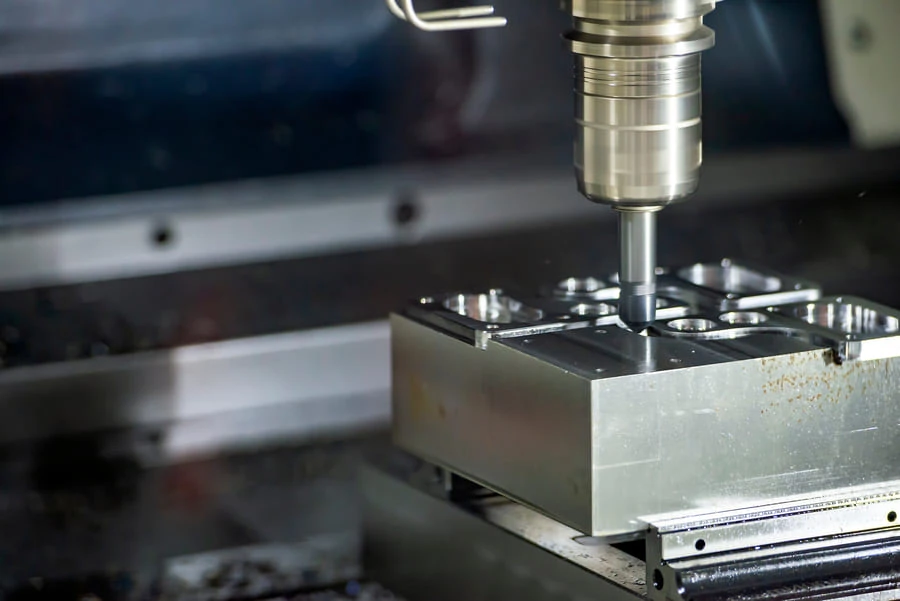
Chamfer milling offers the following benefits.
- It prevents the burs formation.
- This process enhances the rigidity of components.
- It reduces the excessive loss of material.
- It prevents workpiece destruction.
Face Milling
Face milling is a process in which the rotating axis of the cutting tools lies perpendicular or at a right angle to the machining surface.
The cutting creates a smooth and flat surface for the workpiece. This milling process is supported by horizontal milling machines as well as vertical milling machines.
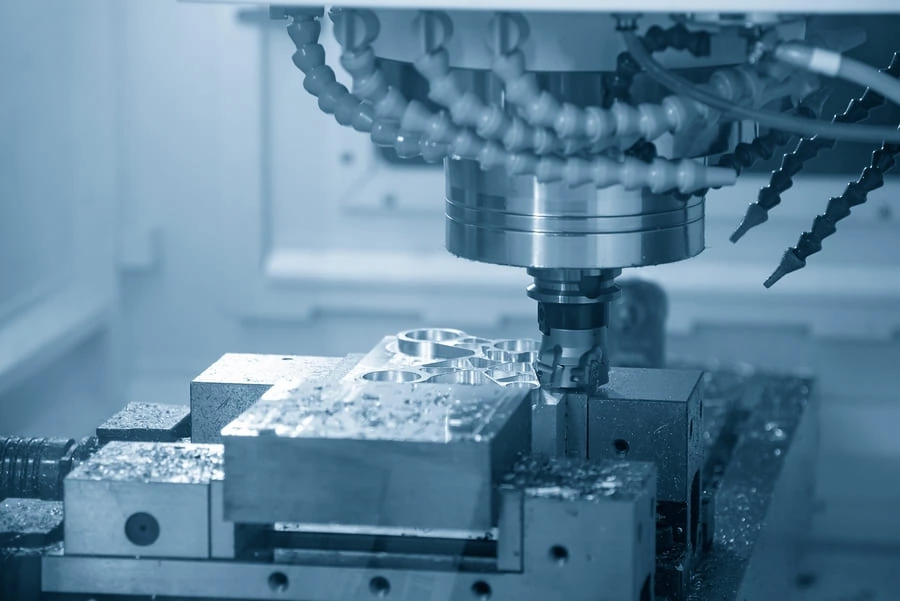
Face milling offers the following benefits.
- It produces an admirable surface finish.
- It helps in achieving greater geometric accuracy.
- The face milling manufacturing process aids in quickly cutting the large-size workpiece.
Angular Milling
Angular milling is the milling of flattened surfaces at a specific angle using a cutting tool. The surface is not positioned perpendicular or parallel to the cutter.
The cutting is done through an angular milling cutter. It is similar to plain milling and differs only due to its angular setup.
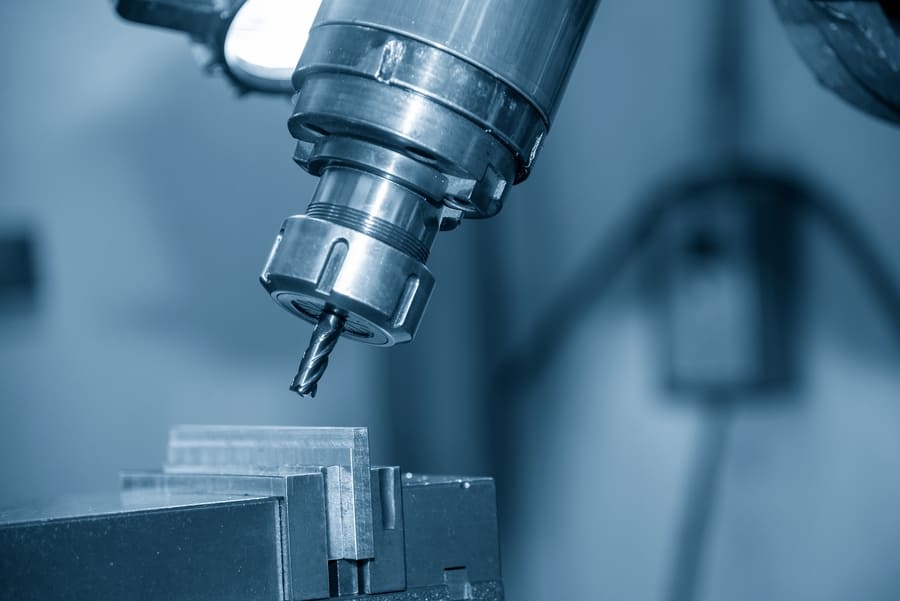
Form Milling
Form milling makes irregular contours, such as curves, on a CNC machined part. It is done using milling cutters having various irregular Concours.
Thus, the Concours can be curved, convex, or concave in the form milling process. To manufacture a product having concave edges, you must use a milling cutter having convex edges.
Slot Milling
Slot milling is a process in which the material is removed from a workpiece by moving the rotating cutters inside and outside the slot.
It is mainly done to create pockets, slots, or keyways using slot milling cutters. It is an extremely useful process for deep-cutting pockets or slots.
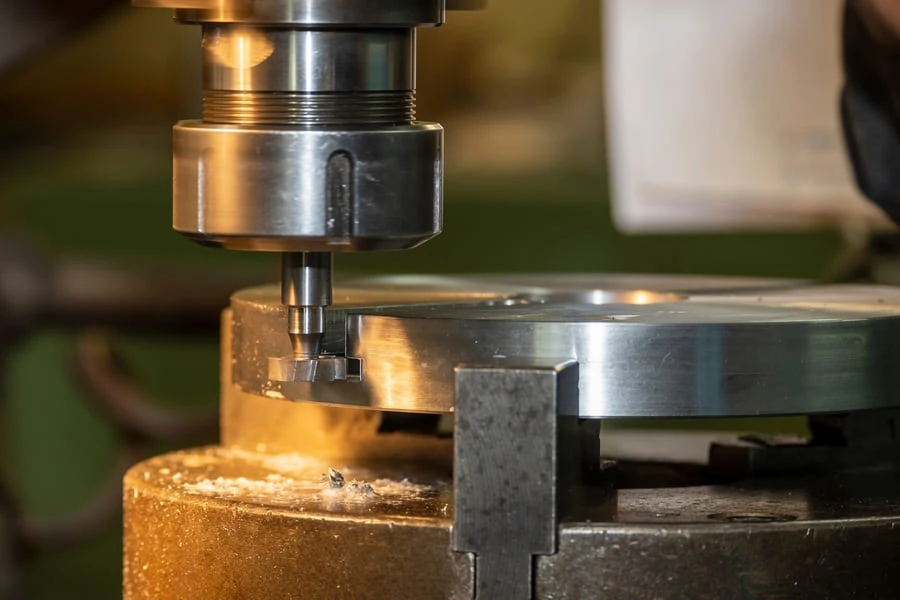
Side Milling
Side milling is a process in which a flat vertical surface is created on the side of a CNC machined part. The cutters used for this purpose are known as side milling cutters.
The rotation of the vertical feed screw of the table sets the cut depth during machining.
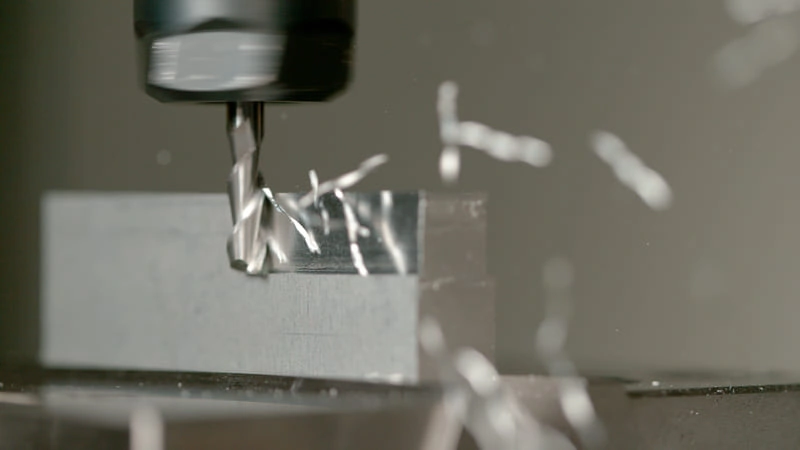
Plain Milling
Plain milling, also named surface or slab milling, is used to mill horizontal or flat surfaces of workpieces. The cutting tool is positioned parallel to the machined parts.
Therefore, the cutting is not done continuously. Instead, the cutter cuts by showing movement from one end of the machined part to the other.
Pros & Cons of CNC Milling
Advantages
1- Greater Precision and Accuracy
The main advantage of the CNC milling process and milling machines is the production of highly accurate and precise final machined parts. This production is due to computer numerical control milling as it eliminates and reduces the chances of errors during machining.
It can produce parts with complex geometries having tight tolerance of 0.0004 mm using various axis milling machines such as 3-axis, 4-axis, and 5-axis milling machines.
2- Suitable for a Large Variety of Materials
You can choose a wide range of materials for the CNC milling process. These materials may include metals, plastics, etc. Therefore, you can use your desired available material to undergo CNC milling.
For the fabrication of small parts, we mostly use vertical milling machines, while for manufacturing large parts, we use horizontal milling machines.
3- Highly Efficient and Quick Process
CNC milling is an efficient process with a large number of cutting tool kits. The cutting tools are exchanged on their own according to requirements during machining. It increases its efficiency and makes it a fast process, reducing production time.
4- Cost-Effective
CNC milling is a cost-effective process as compared to other machining techniques. The components and tools used in this CNC process are less costly than those used in other processes.
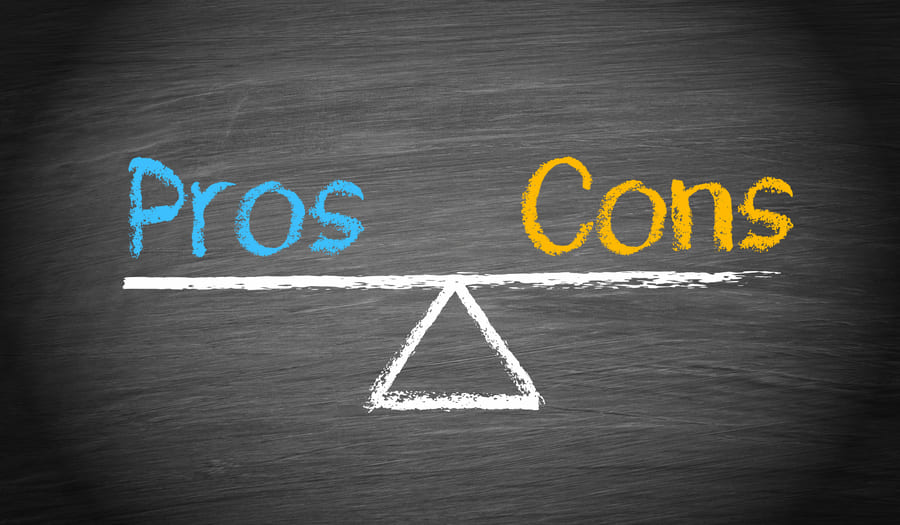
Disadvantages
1- More Production of Material Waste
As we know, the finished end product is produced when you remove material in CNC milling. Therefore, much material waste is produced compared to other manufacturing methods.
2- Not Suitable for Small Amounts of Product
During milling operation, enough time is required for the designing and programming of producing a product with the desired specification. Therefore, it is not considered suitable for manufacturing small quantities of products.
3- Less Availability of Qualified Operators
CNC milling is a computer numerical control milling process; therefore, highly qualified operators are required for the programming and supervision of the CNC milling process to manufacture high-quality components.
But most of the milling machines and machine shops lack qualified technicians to operate a milling machine. It can result in incorrect milling operations, producing poor-quality machined parts.
4- Require High Maintenance
Proper maintenance of CNC milling machines is required for the bulk production of precise and accurate, good-quality machined parts. Poor maintenance can make the machine defective, which may cause disruptive functioning of milling machines.
Common Materials for CNC Milling
The CNC milling process can use a wide range of materials for product manufacturing. Here are some commonly used materials for this purpose.
Metals
You can use a large variety of metals for CNC milling. Some important metals are as follows.
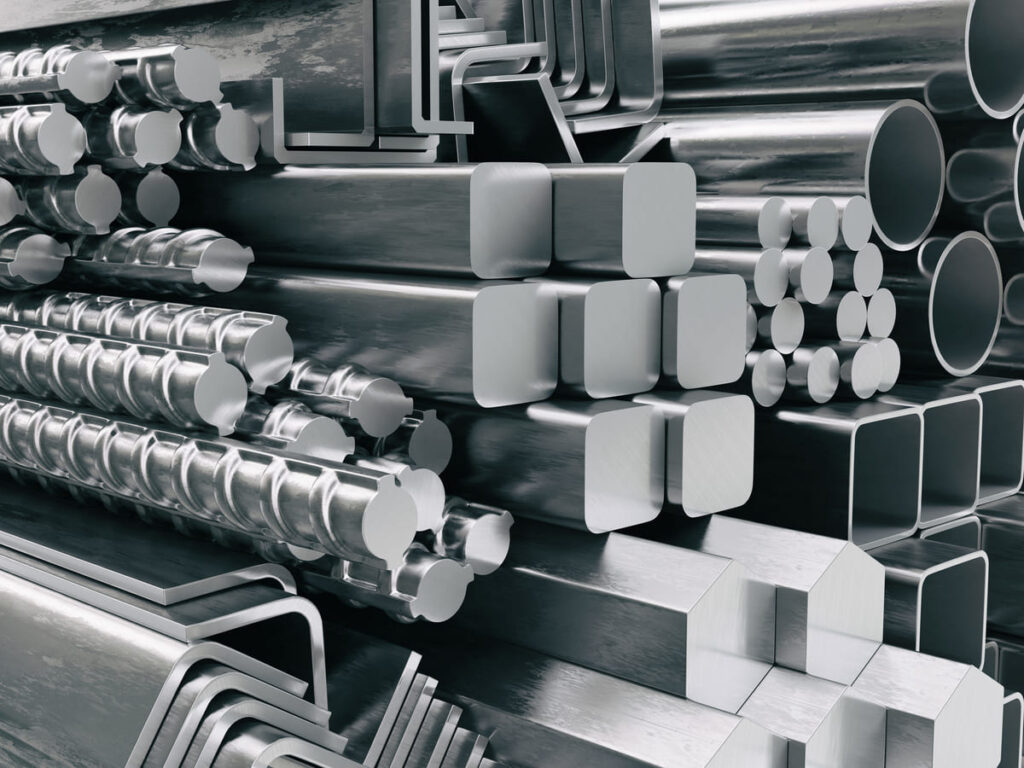
Stainless Steel
Stainless steel is widely adopted for CNC milling because of its following properties.
- Excellent uniformity
- Resistant to corrosion
- Can undergo heat-treatments
- High ductility
- Weldability
- Outstanding machineability
Aluminum
Aluminum is a good choice because it possesses the following features.
- Provides custom finishing due to many options for surface finishing
- Recyclable
- High resistance to corrosion
- Admirable machineability
- Greater strength-to-weight ratio
Brass
Brass is usually prioritized for CNC milling because of the following characteristics.
- Higher strength
- Hardness
- Good machineability
- Remarkable corrosion resistance
- Better overall conductivity
Plastics
In addition to metals, many plastics are used for manufacturing products through CNC milling operations. Some common plastics used for milling are mentioned below.
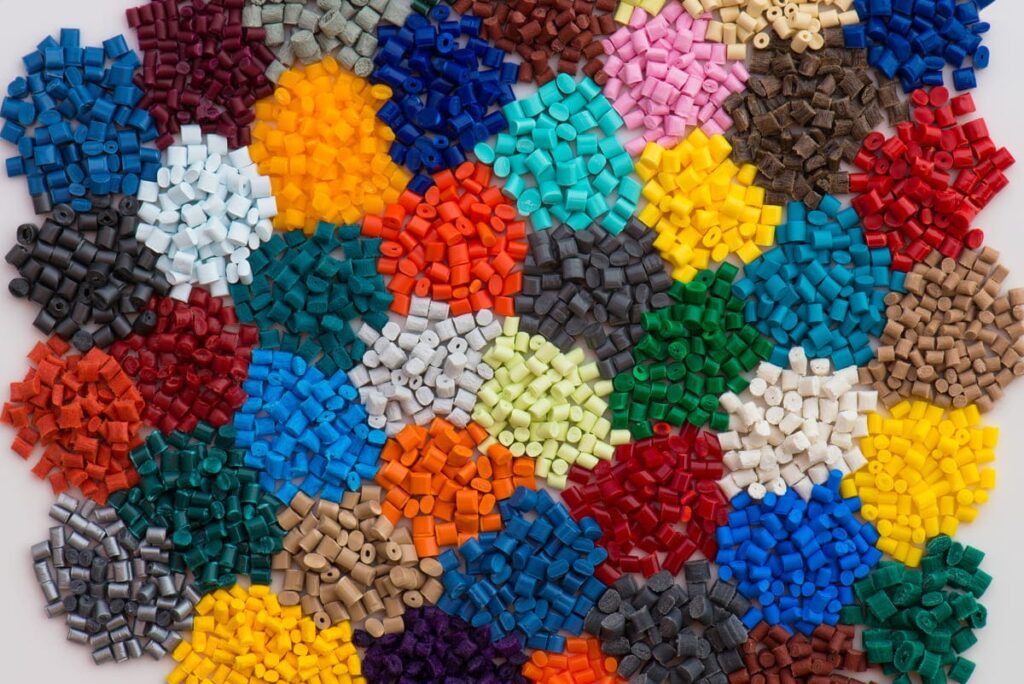
ABS
It is a thermoplastic used for the following reasons.
- Excellent thermal resistant
- Higher strength
- Good machinability
- Cost-effective
Nylon
Nylon is a plastic that undergoes many types of milling machines, like vertical and horizontal milling machines, because of underlying features.
- Tigh tolerance
- Easy machining
- High dimensional stability
- Greater toughness
- Greater strength
PVC
PVC, also known as polyvinyl chloride, is a rigid plastic suitable for CNC milling due to its properties.
- Outstanding dielectric strength
- The low absorption capacity of moisture
- High resistance toward chemicals
- Greater corrosion resistance
In addition to the materials mentioned above, you can also use the following materials for CNC milling because of their excellent milling properties, such as good machineability, corrosion resistance, etc.
- Glass
- Wood
- Ceramics
- Rubber
- Foam
Main Types of CNC Milling Machines
In the CNC milling process, according to the different cutting tool sets used, CNC mill machines are mainly divided into the following types.
Face Mill
Face mills are tools in which cutting edges are present on the side of the cutting head. They are unable to do the axial cutting. Their cutting teeth are made of carbide inserts that can replace.
End Mill
End mills are tools used for axial cutting and possess cutting teeth on both sides. They are manufactured by using cemented carbide or high-speed steel. They are commonly used in plunging etc.
Slab Mill
Slab mills are cutters used for the bulk removal of material from a CNC machined part. They are considered advantageous on the commercial scale.
Ball Cutter
Ball cutter is also recognized as ball-nosed cutters having a hemispherical end. We can use a ball cutter to reduce stress and properly cut 3D shapes.
Involute Gear Cutters
Involute gear cutters are those that help in machining the gears. Thus, it makes it possible to produce gears in CNC milling.
Side and Face Cutter
Side and face cutters are those cutters that bear teeth on a single side and around the circumference. They are mainly used for the milling of grooves and slots.
Hollow Mill
It is also known as a hollow milling cutter. These cutters resemble thick wall pipes and have cutting teeth on their internal surface. They offer applications in screw machines.
Fly Cutter
It is a single-point cutting tool used for machining the flat and larges surfaces of workpieces. It is composed of a central body holding single or two tool bits. It shows similarity to the lathe tool.
Roughing End Mill
These tools bear scallops on their cutting edges. It is beneficial for the breakdown of chips into small parts. They are used for the fast and efficient removal of bulk material.
Shell Mill
A shell mill is a tool having a circular shape and a flat end. Its sides bear carbide or carbide-tipped inserts. It is used for the creation of flattened faces on CNC machined workpieces.
Industrial Applications of CNC Milling
Aerospace
CNC milling is used in aerospace industries to manufacture various aeronautic parts. The resulting parts show greater accuracy and durability.
Automotive
The automotive industry demands machining operations with greater efficiency. Therefore CNC milling is used to create automotive parts, including gearboxes, cylinder heads, exhaust components, etc.
Medical
In the medical industry, CNC milling is used to manufacture parts with specific designs and precision, such as prostheses and implants.
Electronic
CNC milling is used in the electronic industry to manufacture high-precision components. Some electronic parts manufactured through it include sensors, printed circuit boards, etc.
Telecommunication
In the telecommunication industry, CNC milling is used to manufacture components with optimal consistency and precision, such as shieldings, antennae parts, microwave tower components, etc.
Home Decor
CNC milling is widely used for the manufacturing of the home decor components such as furniture, wall art, and other wall-designing products.
Conclusion
As we know, CNC milling is an automated process, producing parts with remarkable features, i.e., greater precision and accuracy by removing material from the workpiece.
Each type of milling machine offers a unique setup to perform various operations.
Different types of milling machines, like horizontal and vertical, are intended to produce various structural components using a wide range of milling machine tools.
Its ability to work with a wide range of materials and flexible processing capabilities make it suitable for manufacturing many industrial components.