CNC machining is a programmable manufacturing process in which the movement of tools and production equipment is controlled by pre-programmed codes and instructions.
In contrast to traditional manual operations, CNC machining processes are controlled by computer programs that manage a complex series of mechanical movements, such as turning, milling, drilling and grinding, to machine precision parts by cutting plastics, metals or composites.
At present, there are many options for multi-axis CNC machining, from 3-axis to 5-axis and even 9-axis.
Listed below is a comparison of the two more popular types of CNC machining in the industry today.

3-axis CNC machining
3-axis CNC machines make cutting tools to move along three linear axes of X, Y and Z to position and exert the cutting operation.
3-axis CNC machining includes CNC milling and CNC turning. Among them, 3-axis CNC milling is very friendly for producing most geometries and simple parts.
In contrast to CNC milling, CNC turning machines parts faster and at a lower cost, which is definitely more suitable for parts with high volume production needs.
Since a 3-axis CNC machine can only cut along three axes, it can have some difficulty in handling irregular shapes or designs with deep, narrow cavities that are difficult to reach.
5-axis CNC machining
5-axis machine has three linear axes of X, Y, Z and two extra rotary axes.
Thanks to its flexible simultaneous multi-axis machining capability, the tool can approach the part from any direction and complete the cut in just one setup.
At the same time, simultaneous 5-axis CNC machining also provides better surface finish and dimensional stability, but it has a high manufacturing cost per unit.
In continuous 5-axis CNC machining, the cutting tool and the workpiece work in conjunction during machining.
It help save machining time and make it ideal for machining complex shapes and precision parts.
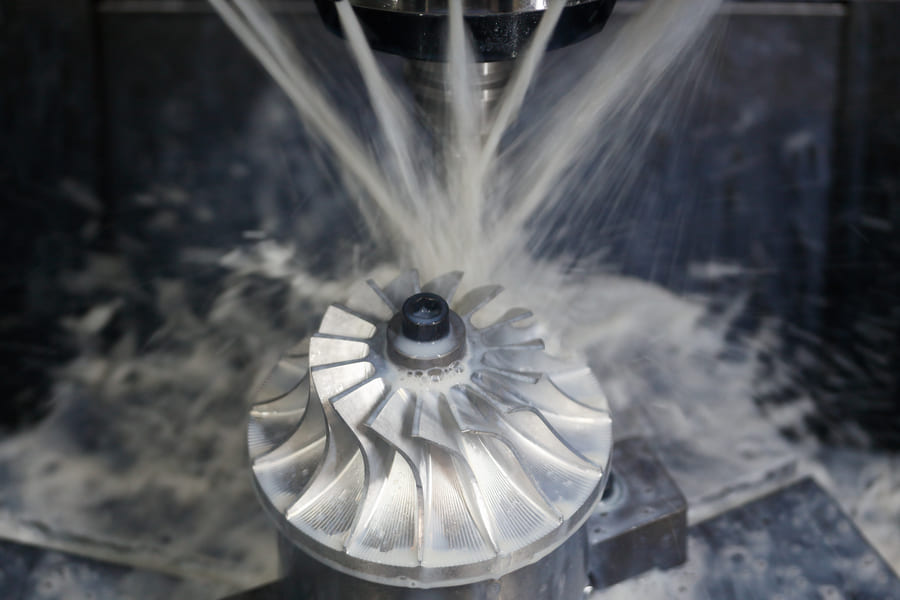
Three types of 5 axis Machining
When it comes to 5-axis machining, it is important to mention 5-side machining.
5-side machining is often mistaken for 5-axis machining.
5-axis machining has five axes of x, y, z, a and b (or c), and they can simultaneously work together.
It is suitable for heterogeneous machining, irregular shape machining, and bevel holes, etc.
While 5-side machining is similar to 3-axis machining, it can only machine five sides, but it cannot do special machining, bevel holes, cutting bevels, etc.
Listed below 3 types of 5-axis machining.
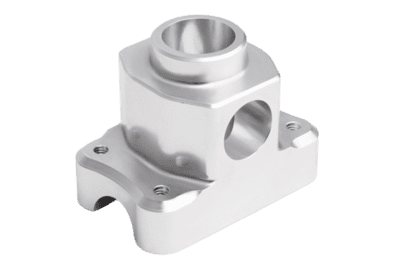
3 + 2 Axis
In 3+2, 3 axes can used for simultaneous operation and the remaining two axes are fixed during machining. The fixed two axes can be changed during the set-up. That means it works as a regular 4- axis VMC after the part setup.
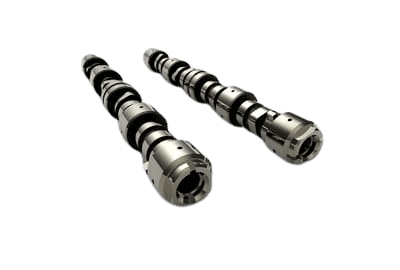
4 + 1 Axis
In 4+1 axis, also known as 4/5 Axis simultaneous machining, 4 axes can be used simultaneously for machining operation and the remaining one is fixed during machining. The fixed axis can be changed during the set-up.
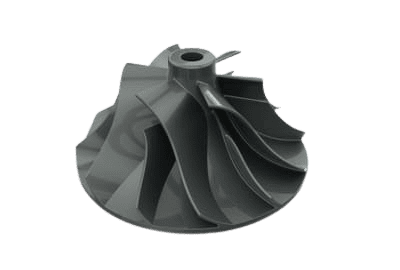
Simultaneous 5 Axis
This is a full 5-axis machine structures in which three linear axes (X, Y and Z) and two rotary axes (A and B) engage synchronously to form simultaneous 5-axis. It help the cutting tool to approach the part from any direction.
3-axis machining vs. 5-axis machining
Whether it is 3-axis CNC machining or 5-axis CNC machining, they all have their own advantages and disadvantages.
When choosing a machining solution, the most suitable one should be selected according to the actual situation of the project.
It requires comprehensive consideration of factors such as machining difficulty, machining accuracy, programming difficulty, machining cost and machining efficiency, and finding an equilibrium.
If you need to cut a flat side, 3-axis machining may be your preferred choice.
In addition to being more affordable than 5-axis machining, 3-axis machining is simpler to program and, therefore, does not entail excessive costs. And, the machining time for 3-axis machining is shorter.
If you need to machine more complex parts, then it is necessary to consider 5-axis machining.
Five-axis machines offer more advanced and flexible machining capabilities that allow for higher accuracy and greater freedom of movement, but often their machining costs are higher as well.
Work with Sindparts
As a trusted CNC machining partner, Sindparts not only has high quality precision machining capabilities, but will also provide you with the most satisfying service and the best cost-effective manufacturing solutions in our partnership.
We will help you grow your profits.